1 RH 機(jī)械泵真空系統(tǒng)的構(gòu)成
RH 精煉全稱 RH 真空循環(huán)脫氣精煉法,具有處理周期短,生產(chǎn)能力大,精煉效果好等優(yōu)點(diǎn),適合冶煉周期短,生產(chǎn)能力大的轉(zhuǎn)爐工廠采用。
常規(guī)的 RH 真空精煉設(shè)備均采用多級水蒸氣噴射泵系統(tǒng)作為真空獲取方式,由于近年來國家大力推進(jìn)鋼鐵行業(yè)節(jié)能減排,工業(yè)電價(jià)比蒸汽有更低的成本優(yōu)勢,由羅茨泵 + 螺桿泵組合的機(jī)械泵抽氣系統(tǒng)受到越來越多的青睞。本文以國內(nèi)某鋼廠 210tRH 真空精煉設(shè)備機(jī)械泵抽氣系統(tǒng)為例闡述:該系統(tǒng)由布袋除塵器、主抽氣管道,24 臺(tái)一級羅茨真空泵、24 臺(tái)二級羅茨真空泵、24 臺(tái)三級羅茨真空泵及 12 臺(tái)四級螺桿泵構(gòu)成,系統(tǒng)抽氣能力為 1100000m 3 /h(在 67Pa 工作壓力下)。如圖 1,圖 2 所示。
相比于蒸汽噴射泵真空抽氣系統(tǒng),機(jī)械真空泵抽氣系統(tǒng)具有真空泵數(shù)量多、排布緊密、法蘭連接多等特點(diǎn),潛在漏氣點(diǎn)多,真空系統(tǒng)檢漏困難。
為了獲得較好的真空精煉效果,RH 精煉爐真空處理時(shí)真空室內(nèi)的工作真空度需達(dá)到 67Pa 以上,真空系統(tǒng)的允許漏率≤50kg/h(一般要求允許漏率小于真空系統(tǒng)抽氣能力的 10%),因此真空檢漏工作至關(guān)重要。
2 傳統(tǒng)漏率檢測方案及其應(yīng)用在機(jī)械
真空泵系統(tǒng)上的劣勢和難點(diǎn)
對于蒸汽噴射泵真空系統(tǒng),因其機(jī)械結(jié)構(gòu)簡單,法蘭連接少,潛在漏點(diǎn)少,因此相對容易檢漏。
實(shí)際工程中多采用正壓檢漏及負(fù)壓驗(yàn)證的聯(lián)合檢漏法,該法的流程是:用正壓檢漏的方法先檢驗(yàn)真空系統(tǒng)的密封性(即用適當(dāng)壓力的壓縮空氣充入系統(tǒng)后,保壓 24 小時(shí),計(jì)算其實(shí)際泄漏值,檢測合格后抽真空進(jìn)行負(fù)壓檢漏。
我們對封閉真空系統(tǒng)進(jìn)行正壓氣密性試驗(yàn),向封閉系統(tǒng)通入 0.15MPa(表壓)的壓縮空氣,待壓力穩(wěn)定后:
①斷氣源,穩(wěn)壓 24 小時(shí);
②觀察 24 小時(shí)內(nèi)壓力的變化情況,并做好相關(guān)記錄。
假定經(jīng)過 24 小時(shí)的氣密性試驗(yàn),壓力下降值為 ΔP,起始時(shí)氣體壓力為 0.15MPa;根據(jù)公式(1)計(jì)算氣體平均泄漏率:
M=
ΔP
24P
Vρ (1)
式中:M—— — 泄漏量,單位 kg/h;
V—— — 密閉體的體積,單位 m 3 ;
ρ—— — 標(biāo)準(zhǔn)大氣壓下空氣密度,單位kg/m 3 ;
P—— — 起始壓力,單位 Pa;
ΔP—— — 壓力下降值,單位 Pa。
上式計(jì)算出的泄漏量 M,即系統(tǒng)每小時(shí)泄漏的質(zhì)量流量。若泄漏量 M 遠(yuǎn)小于 50kg/h 的設(shè)計(jì)泄漏量,則正壓氣密性試驗(yàn)合格,之后對真空系統(tǒng)抽真空進(jìn)行負(fù)壓驗(yàn)證。
對于機(jī)械真空泵抽氣系統(tǒng),由于其系統(tǒng)容積大,管道排列復(fù)雜,閥門多,羅茨泵及螺桿泵的結(jié)構(gòu)(泵油及密封件的存在)采用正壓檢漏并不合適,因此只能考慮負(fù)壓檢漏,然而粗低真空范圍無法使用檢漏儀,如何快速找到漏氣區(qū)域確定漏點(diǎn)至關(guān)重要。
結(jié)合多年 RH 真空系統(tǒng)調(diào)試經(jīng)驗(yàn),我們提出機(jī)械真空系統(tǒng)負(fù)壓分段檢漏方案,圖 3 為真空
泵系統(tǒng)示意圖。該真空泵系統(tǒng)由真空室、真空主閥、真空旋風(fēng)除塵器、真空袋式除塵器、一級羅茨真空泵、二級羅茨真空泵、三級羅茨真空泵及四級螺桿泵構(gòu)成(簡化起見,每級真空泵機(jī)組在示意圖中均由一臺(tái)真空泵表示),在每一級真空泵進(jìn)氣口均有一臺(tái)氣動(dòng)真空切斷閥及一臺(tái)絕壓力變送器,在工作時(shí)顯示各級泵的真空度。
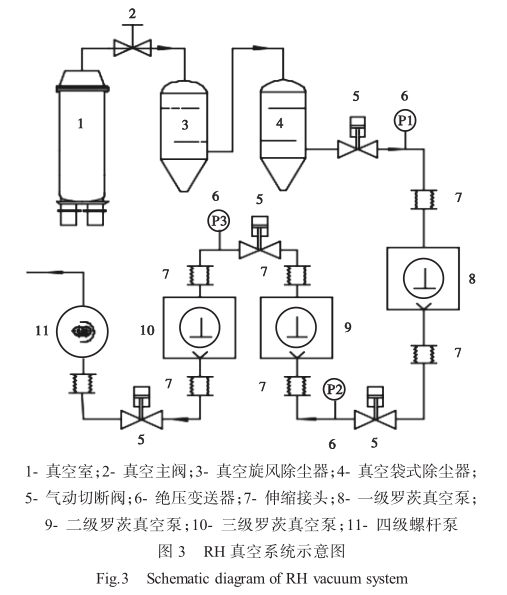
3 機(jī)械真空泵系統(tǒng)檢漏方案
3.1 檢漏方法
最適合 RH 機(jī)械泵抽氣系統(tǒng)的負(fù)壓檢漏方法是靜態(tài)升壓法 [10] ,首先將真空系統(tǒng)抽至 2kPa,關(guān)閉真空主閥及末級泵進(jìn)口閥門將真空系統(tǒng)同真空室隔離,關(guān)閉真空泵,使用絕壓變送器測量抽氣管道內(nèi)壓力變化。假設(shè)被測容器體積為 V,在時(shí)間間隔 ΔT 內(nèi)測到的壓升為 ΔP,忽略容器內(nèi)的放氣,則容器的總漏率為:
Q L =VΔP/ΔT
考慮將系統(tǒng)分為四部分:主閥至一級泵進(jìn)氣口閥門區(qū)域?yàn)?V 1 、一級泵至二級泵進(jìn)氣口閥門區(qū)域 V 2 、二級泵至三級泵進(jìn)氣口閥門區(qū)域 V 3 、三級泵至四級泵進(jìn)氣口閥門區(qū)域 V 4 ,則:
Q L =(V 1 +V 2 +V 3 +V 4 )ΔP/ΔT式中:V 1 >V 2 >V 3 >V 4 ,若打開各級真空泵進(jìn)氣真空閥門,理想狀況下,各段的壓升 ΔP 是相同的,即:
Q L =(V 1 ΔP+V 2 ΔP+V 3 ΔP+V 4 ΔP)/ΔT下面關(guān)閉每一級真空泵進(jìn)氣閥門,忽略真空閥門之間的內(nèi)漏,由于每一段各自漏孔漏率的不同,實(shí)測的 ΔP 有所不同,假設(shè) V 1 區(qū)域壓升ΔP 1 ,V 2 區(qū)域壓升 ΔP 2 ,V 3 區(qū)域壓升 ΔP 3 ,V 4 區(qū)域壓升 ΔP 4 ,則有:
Q L =(V 1 ΔP 1 +V 2 ΔP 2 +V 3 ΔP 3 +V 4 ΔP 4 )/ΔT=VΔP/ΔT分類討論如下:
(1) 若出現(xiàn) ΔP 1 >ΔP、ΔP 2 >ΔP、ΔP 3 >ΔP、ΔP 4 >ΔP 或 ΔP 1 <ΔP、ΔP 2 <ΔP、ΔP 3 <ΔP、ΔP 4 <ΔP,從上式可以看出不滿足公式要求,則首先考慮儀表的準(zhǔn)確性問題。
(2)若 ΔP 1 >ΔP>ΔP 2 >ΔP 3 >ΔP 4 ,則證明系統(tǒng)漏氣主要集中 V 1 段,V 2 、V 3 、V 4 段相對較小,應(yīng)對 V 1 段進(jìn)行重點(diǎn)檢漏,發(fā)現(xiàn)漏點(diǎn)封堵后重復(fù)以上步驟。
(3)若 ΔP 1 >ΔP 2 >ΔP>ΔP 3 >ΔP 4 ,則證明系統(tǒng)漏氣主要集中在 V 1 、V 2 段,V 3 、V 4 段相對較小,由于 V 1 >V 2 ,表明 V 1 部分的漏孔更大,應(yīng)優(yōu)先檢查 V 1 ,而后檢查 V 2 ,檢查的重點(diǎn)應(yīng)放在大的法蘭接口及環(huán)形焊縫處。
由于真空系統(tǒng)體積巨大,氣動(dòng)閥門,機(jī)械冷卻水,介質(zhì)氣體的存在對檢漏工作干擾很大,因此在檢漏時(shí)應(yīng)在系統(tǒng)安全的情況下關(guān)閉氣動(dòng)閥門供氣球閥,機(jī)械泵冷卻水進(jìn)回水及介質(zhì)氣體。
表 1 為利用上述方法檢漏后得出的實(shí)測數(shù)據(jù),該檢漏方法能極大減少檢漏時(shí)間,為檢漏工作帶來便利。
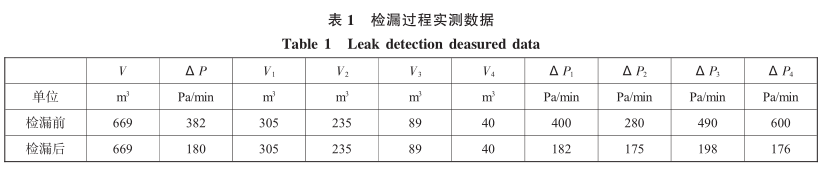
3.2 漏孔當(dāng)量計(jì)算
檢漏完成后,需要對系統(tǒng)實(shí)際漏率進(jìn)行測算,
我們引入真空系統(tǒng)性能分析室,分析室位于真空主閥之后,真空旋風(fēng)除塵器之前,通過管道連接至真空系統(tǒng)。分析室有若干標(biāo)準(zhǔn)質(zhì)量流量噴嘴漏孔,進(jìn)行漏率測試前,首先將真空系統(tǒng)抽至2kPa,關(guān)閉真空主閥,計(jì)算檢漏后系統(tǒng)漏率為X(kg/h)時(shí)引起的系統(tǒng)壓升速率 Y(Pa/min)。破空后,再次將真空系統(tǒng)抽至 2kPa,打開 50kg/h 標(biāo)準(zhǔn)漏孔,產(chǎn)生人為泄漏率,由泄漏量 X+50(kg/h)引起的壓升可計(jì)算為 Z(Pa/min),那么實(shí)際泄漏率X 可由下式計(jì)算:
X=50×Y÷(Z- Y)kg/h
若 X≤50kg/h,則證明真空系統(tǒng)的漏率滿足工藝要求。
當(dāng)量漏孔的大小使用下式來進(jìn)行計(jì)算,由于粗低真空漏率較大,因此流動(dòng)多為粘滯流,根據(jù)一維定常等熵流動(dòng)的伯努利方程,質(zhì)量流量 G與漏孔 d 之間的關(guān)系為:
4 真空系統(tǒng)檢漏的智能化控制模型
近年來,關(guān)于真空系統(tǒng)抽氣過程的理論計(jì)算及仿真模擬及真空冶煉過程中的底吹氬循環(huán)模擬已做過大量深入研究,但對于大型真空系統(tǒng)智能化檢漏研究相對較少 。
根據(jù)分段檢漏原理,提出機(jī)械真空泵抽氣系統(tǒng)智能化檢漏模型,采用逐級定壓自動(dòng)控制方法啟動(dòng)自動(dòng)檢漏程序,系統(tǒng)抽真空至目標(biāo)真空度,記錄設(shè)定時(shí)間內(nèi)被測系統(tǒng)壓力變化值,利用“靜態(tài)壓升法”,定量計(jì)算得到泄漏率,重新將系統(tǒng)抽至目標(biāo)真空度,記錄各級真空度變化值,定性判斷漏氣點(diǎn)大概位置,完成檢漏工作后測試,計(jì)算系統(tǒng)漏率,超過設(shè)定差值,報(bào)警。圖 4 為該模型流程框圖。
5 結(jié)論
本文通過分析蒸汽噴射泵正壓檢漏方法及該法應(yīng)用在機(jī)械泵真空泵系統(tǒng)上的困難,給出了如下結(jié)論:(1) 大型機(jī)械真空泵真空系統(tǒng)更適合負(fù)壓檢漏,分段檢漏法更加實(shí)用高效。(2)分段檢漏法的理論分析,能很好地指導(dǎo)實(shí)際檢漏過程。
(3)通過測算真空系統(tǒng)的實(shí)際漏率,計(jì)算出當(dāng)量漏孔大小。(4)給出了機(jī)械泵真空系統(tǒng)智能化檢漏模型,可快速判斷漏氣點(diǎn)大致位置,提高真空系統(tǒng)檢漏效率。